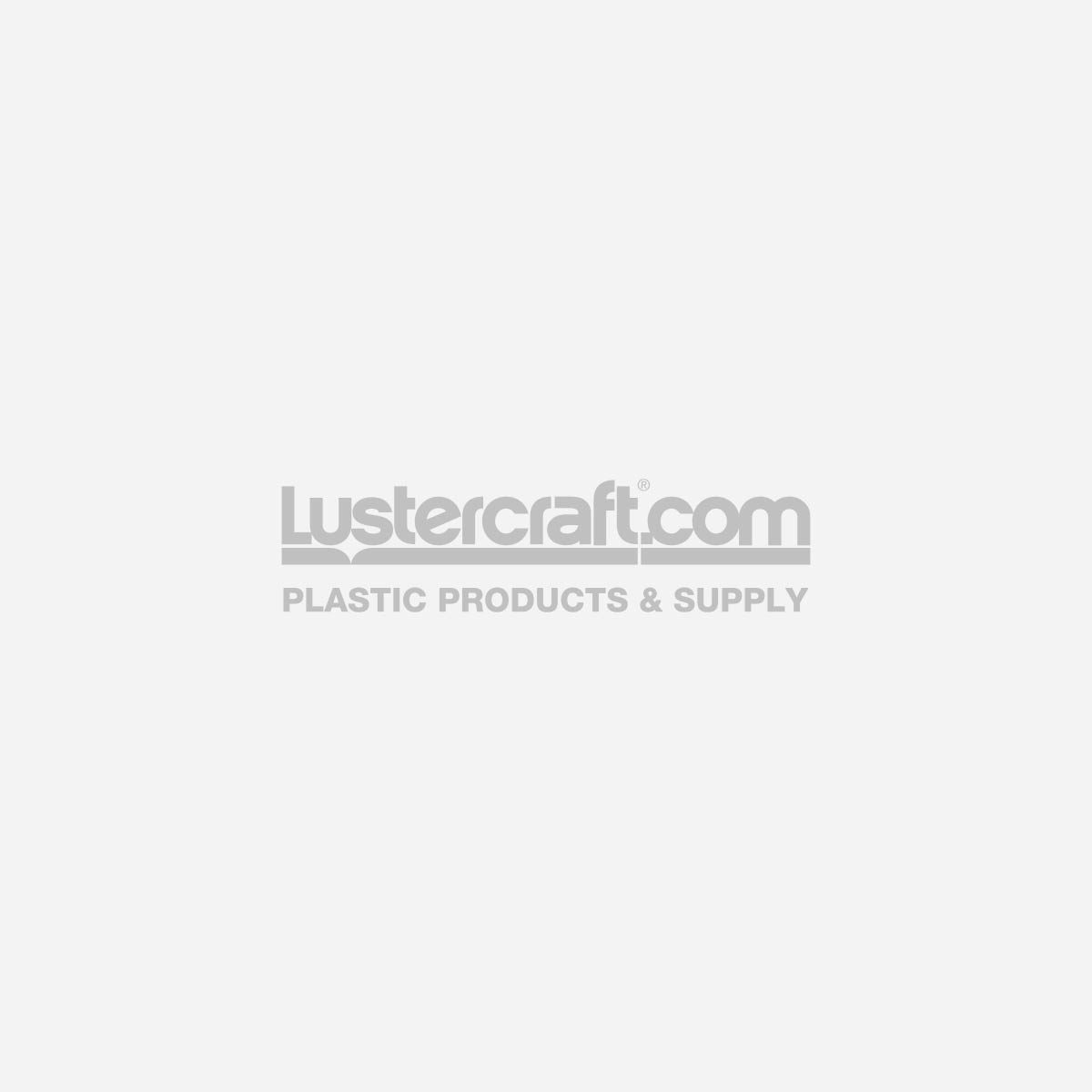
Different grades of PVC
Sawing
High-speed bandsaws and circular saws with a cutting speed of up to 3000 m/min are recommended. Depending on the thickness of the sheets, saw blades with a tooth pitch of between 5 and 10 mm are used. For circular saws, it is normally recommended to use blades with a tooth geometry that alternates between flat teeth, trapezoidal teeth and carbide-tipped teeth. The saw blade diameter and the number of teeth must be coordinated to match the material to be machined, the machine type and the machine speed.
In order to obtain clean edges to cuts and to avoid cracking, always clamp the sheet material in the workholding fixture so that it does not vibrate. This is very important for thin sheets with a thickness of 1–3 mm, not only when machining them singly but also in stacks. Use guillotine shears to cut a thickness of 1 mm. In the case of jigsaws, use only sharpened, unset saw blades. The feed (manual) must be at a slow, and constant speed.
Drilling
All Rigid Foam PVC sheets in question can be drilled using the sort of twist drills familiar from drilling metals whose angle of twist is approx. 30°. The point (or nose) angle can be up to approx. 110°, while the lip relief angle should be no smaller than 12–16°. The cutting and feed speeds depend on the depth of the hole to be drilled: the thicker the sheet, the slower the speed. For holes larger than 20 mm in diameter, two-flutecutters with pilots are used. Holes larger than 40 mm in diameter are cut using circular cutters.
Turning
When rough turning, it is advisable to combine a slow feed rate with a greater cutting depth and to use a cutting tip with a radius of at least 0.5 mm in order to obtain a groove-free surface. The cutting depth should be max. 2 mm for fine turning. If a faster feed rate is selected, cracking of the material can be avoided by setting a slower cutting speed.
Milling
The milling tools have to be ground so that they are suitable for working the plastic material. They must also provide enough space for an adequate volume of chips. Working with a fast forward feed rate along with moderate cutting speed and deep cuts will lead to good results.
Cutting, Punching, Perforating
Rigid Foam PVC sheets up to 3 mm thick can be cut with guillotine (sheet) shears. The cut must be made swiftly and without interruption. The sheets should have room temperature, of at least 20 °C. Thicker sheets (> 3 mm) should be cut using a saw. PVC sheets up to 3 mm thick can be punched and perforated with profiling knives or two-piece tools. Also recommended are punching tools (made of strip steel) with facet cut (bevelled edge) on both sides. Heating the PVC material to 30 to 40 °C is useful and helps aid the working process.