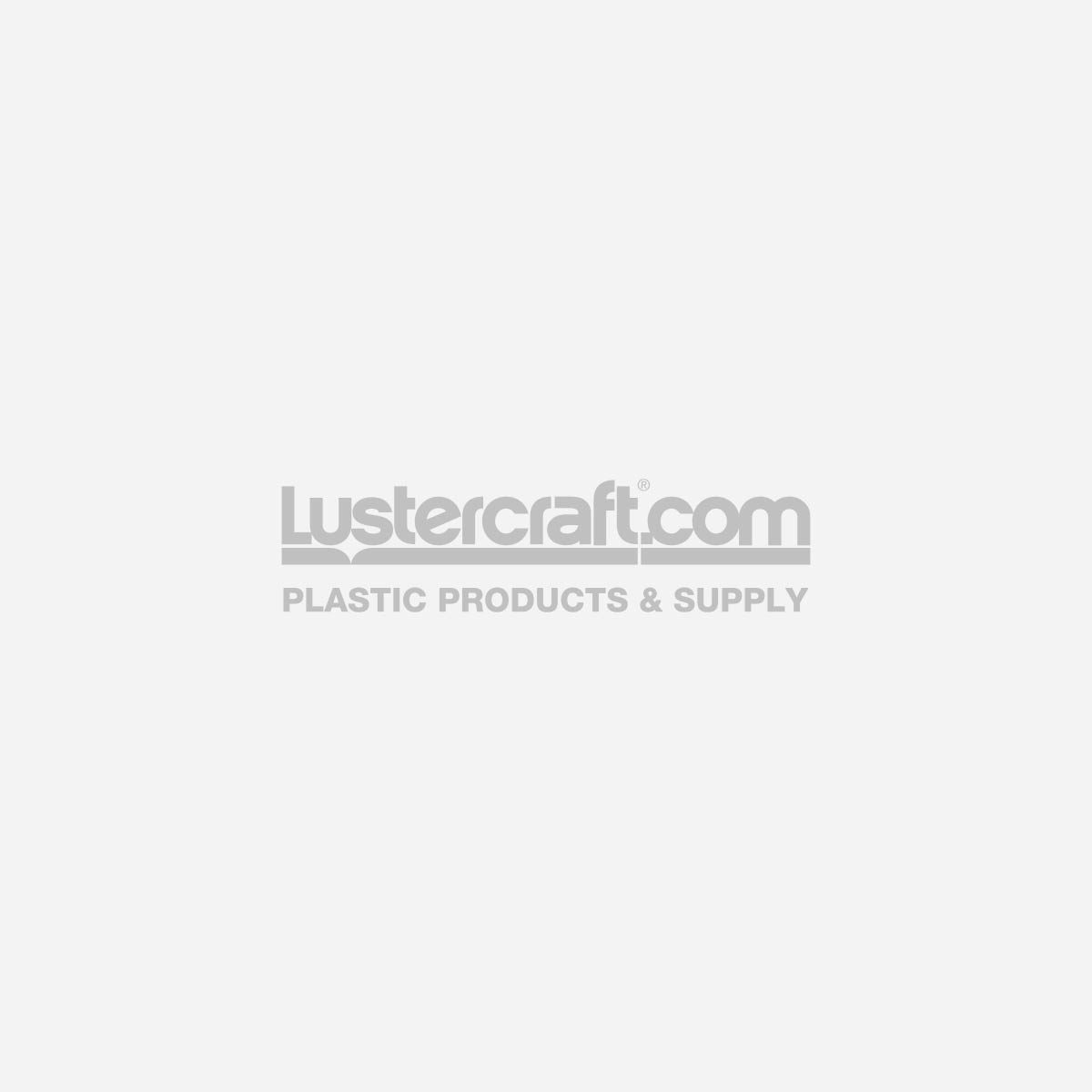
Different Grades of Polyethylene
Cutting
Polyethylene material can be cut with a table saw, radial arm saw, CNC router, band saw, or panel saw. With any cutting process, the key is good sharp tools and adequate chip removal, which helps eliminate heat build-up. A dull tool or improper feed rate can lead to rough edges and heat build-up to the point where the chips start to melt and refuse. It is recommended to always cut a test piece prior to a production run.
Routing
Plastic materials can have a wide variety of machining characteristics ranging from flexible or rigid, soft, and hard. During the routing process, hard plastic forms a splintered wedge or granulated chip, while soft plastic forms a curled chip. Seaboard and a few other grades of Polyethylene do tend to be soft. This represents a unique set of machining circumstances and tool selection opportunities.
Drilling
In order to prevent chip wrap in soft plastics, and crazing in hard materials, it is recommended that the point angle is set between 90° – 110° degrees. Onsrud Cutter has developed a drill with a 60°-degree point and a flat rake face providing the best plunge point in a wide variety of plastics. The point “s” style creates a chip in soft plastics that is easily ejected and allows the use of normal drilling routines during programming. Material such as polyethylene required a peck drilling cycle to prevent the formation of long chips that would wrap around the drill. The elimination of pecking drilling procedures in a program can lead to reduced cycle time and can increase cutter life significantly.
Tips
- For best results, drill bits should ALWAYS be kept sharp.
- Avoid straight plunge cuts into the material. Program the tool path to ramp into, or enter, the material from the side providing a path for the chips to be ejected.
- Maximize dust collection to evacuate gummy chip produced by softer plastics.
- As material thickness increases, so should the diameter of the tool. Larger diameters are less susceptible to vibration and afford better chip removal.
- Ensure part rigidity by following proper Spoil board techniques.
Milling
HDPE can be milled by using the following guidelines:
- Relief angle: 5° to 10° degrees
- Rake angle: -10° to 0° degrees
- Cutting speed: 3,000 to 3,500 feet per minute
- Cutting feed: 0.12″ inches per revolution
Turning
HDPE sheet can be easily machined on lathes using tools that have been ground down to work on plastics, with the following guidelines:
- Setting angle: 5° to 15° degrees
- Rake angle: 0° to 20° degrees
- Adjustable rake angle: 45° to 60° degrees
- Cutting speed: up to 1640 ft./min