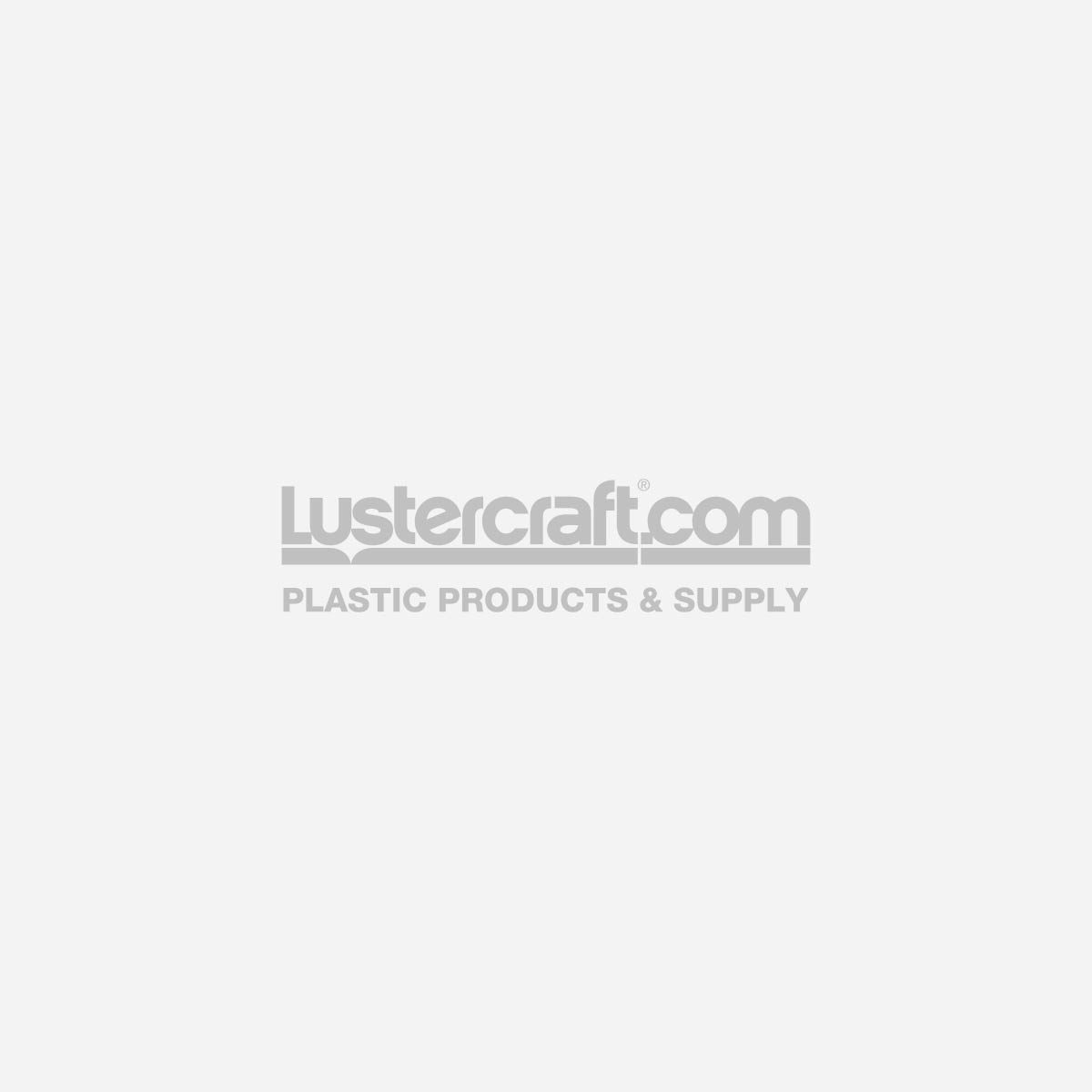
Cast vs. Extruded Acrylic
Cast Acrylic
Manufacturing Process
Unreacted Acrylic (liquid monomer) is poured between twgasketed plates of glass (the cell). The glass is then separated from the cured (reactivated) acrylic.
Benefits of Cast Acrylic
- Superior optical clarity
- Low minimum run/order quantities
- Custom colors available
- Greater range of available thicknesses
- Slightly better chemical resistance than Extruded Acrylic
- Fabricates better
- Slightly higher service temperature than Extruded Acrylic
- Works well tcontain water
- Mechanically Stronger than Extruded Acrylic
- More scratch resistant than Extruded Acrylic
- Polishes easily
Cons
- More expensive than Extruded Acrylic
- Extruded Acrylic
- Manufacturing process:
- Continuously manufactured, not unlike playdough between twrolling pins.
- Benefits of Extruded Acrylic
- Far lower cost than Cast Acrylic
- Accurate, consistent thickness
- Better thickness tolerance
- Cements and thermoforms faster than Cast Acrylic sheets
- Easier tflame polish
- Excellent optical properties
- Good electrical and UV resistivity
- Higher tolerance when heated or bent
Extruded Acrylic
Manufacturing process
Continuously manufactured, not unlike play-doh® between two rolling pins.
- Benefits of Extruded Acrylic
- Far lower cost than Cast Acrylic
- Accurate, consistent thickness
- Better thickness tolerance
- Cements and thermoforms faster than Cast Acrylic sheets
- Easier tflame polish
- Excellent optical properties
- Good electrical and UV resistivity
- Higher tolerance when heated or bent